Although brick has been used as a building material for thousands of years, many homeowners looking to move away from vinyl. Are surprised to learn that various bricks are available and that only some of these bricks are made from clay. Now, the majority of bricks are made from clay, and they are manufactured in industrial-sized furnaces. In earlier times, bricks were made at clay pits that were returned to agricultural use when the clay layers were exhausted. During this period, all the brickmakers travelled to construction sites to produce bricks using local clay.
Bricks in the 18th century were made on brick makers construction sites; thus, the colonial brick makers lived a nomadic existence, moving from one project to another. All bricks were made by hand until the mid-1830s, when Nathaniel Adams (1797-1862), came to Philadelphia from a region. Producing bricks in the Hudson Valley invented the shaping machine; in about 1840 by Nathaniel Adams (1797-1862). Installed the horse-powered machinery at a brickyard in Philadelphia City. In the middle of the 19th century, the development of automatic brick making machines, such as the Bradley & Craven Ltd. Rigid-plastic brick making machine, revolutionised the brick making process. Nevertheless, brick building remained fashionable for most of the early twentieth century until the availability of new construction materials. Mostly, cement and steel surpassed brick usage in construction.
The availability of local clay allowed for a thriving brick manufacturer Australia industry, and brick became one of the region’s most prominent Construction materials. This was particularly the case early on when firebricks required only sufficient bricks to construct the furnace. Above all, an ample supply of clay. Brick makers would excavate the clay, let it cure, harden, shape, allow to dry, and then fire the bricks in the kiln. The drying process would most famously be used for the Fletton Bricks, made from a specific clay. Not only did it not need water, it contained naturally occurring fuel oil (making it cheaper to burn). The clay was mixed to create a sandstone, which was mixed to create clay that was used in making Fletton Bricks.
Firebricks are also refractory bricks made from a specific kind of clay known as sulphur, mainly containing silica and alumina. Typically used for interior walling or for making facades and fencing, sun-dried clay bricks are made of durable cement. Sun-dried clay bricks are also shaped in more uniform patterns than some bricks due to being cast into machine moulds. However, DIYers need to remember that these plain clay sun-dried bricks are the weakest and least durable brick types, so they should never be used as a load-bearing support or foundation.
Professionals can create Sun-Dried Clay Bricks on-site using the standard one-part cement, two-part sand, and four-part aggregate mixture. Some homebuilders may prefer to do these more uncomplicated sun-dried clay bricks. They were used as early as 7,000 B.C. in southern Turkey and around the town of Jericho in present-day Palestine. These bricks are samples of the available materials used in brick making. Researchers frequently experiment with changing levels of clay, sand, lime, fly ash, and cement. Other materials within a given brick to find combinations that offer the best properties. Bricklayers do not produce bricks but do produce mortar, also on-site, with a mixture of mainly lime and sand.
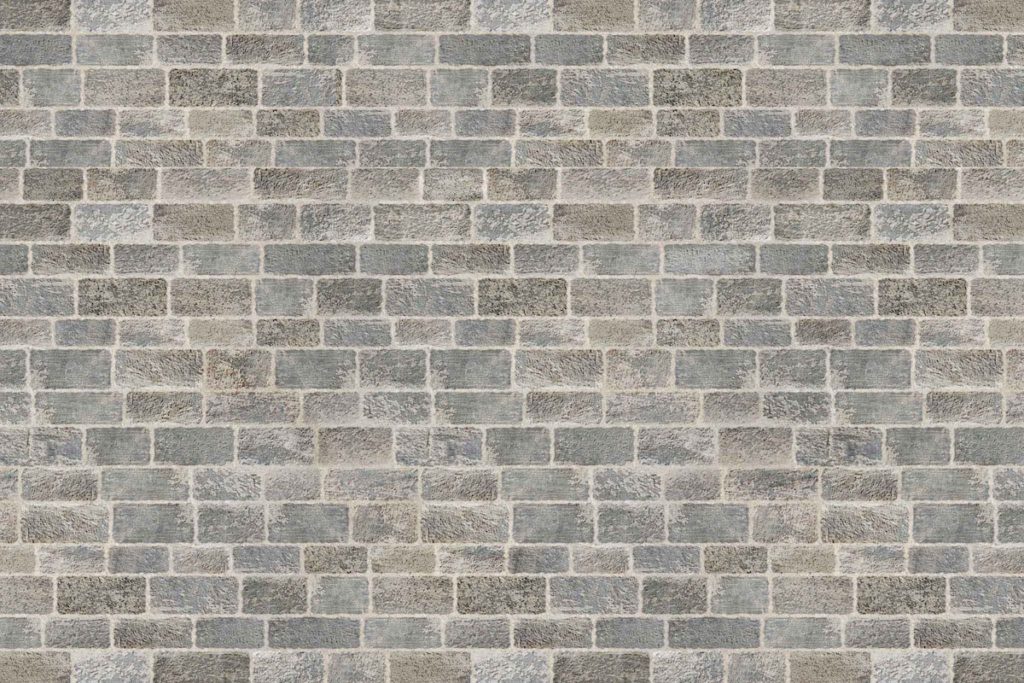
The pressing machines also had the advantage of working with partly dried bricks rather than the harder-to-work-with wet clays. However, they needed help getting the clay to fit in moulds hard enough to push out all of the air and produce properly formed bricks. Yet light enough, so the clay did not stick to the machine. At the same time, some inventors were trying to fix the problem of getting the engine to produce bricks. Others were working on a somewhat different issue of making clay. Stomping through clay pits, the dirty joy for children and adult visitors at Colonial Williamsburg, was a laborious but only method for mixing clay to form bricks in an age before machines.
The deposited clay, mixed with water and sand, produced high-quality bricks, sustaining the Connecticuts brick making industry for over 100 years. Brick making declined when clay deposits were exhausted, and cement blocks became more cost-effective. Still, bricks made locally, with local brick makers, made Philadelphia’s signature built environments possible and those in the surrounding area. Mechanisation came to brick making in the 1820s, and with improvements to transportation. Infrastructure first canals, and later railroads–permanent brickyards. There were moulds for cope bricks, and the half circles were used for water diversion. Water table bricks, used where the foundations and ground floors met; square paves bricks; and compasses bricks, roughly wedge-shaped, used to form circles.